3-D Printing Nuclear Reactors
The nuclear renaissance must import new technologies
-
-
Share
-
Share via Twitter -
Share via Facebook -
Share via Email
-
John Muir famously explained that “when we try to pick out anything by itself, we find it hitched to everything else in the Universe.” Muir was a naturalist, remembered for his role in helping to establish Yosemite National Park, but he might just as well have been talking about technological progress. The idea that everything is interconnected also applies to nuclear energy, which is striving to better hitch itself to other technologies.
Interconnectedness, and piggybacking on each other, is how technologies advance, especially those that are no longer on the cutting edge of industrial progress. Nuclear energy, both in legacy plants and in the advanced reactors moving toward deployment, is currently trying hard to incorporate tools from outside the field—notably Additive Manufacturing (3-D printing), and Artificial Intelligence. But as with a lot of other nuclear projects, progress is somewhere between deliberate and just plain slow
There was a milestone of sorts in December, when Framatome, the French nuclear company, said it had put 3-D printed parts into Ringhals 4, a large pressurized-water reactor in Sweden, which began operations 41 years ago.
The technology may be important for sustaining the operation of legacy reactors, but also shows great promise for new ones. BWXT, working on NASA projects, and the University of Tennessee, as part of the Energy Department’s Transformational Challenge Reactor program, have both sought to marry cutting-edge computing and manufacturing technologies for the benefit of nuclear energy. Parts for old reactors are expensive or unavailable; new ones demand parts that conventional manufacturing can’t supply. So 3-D printing will likely play a key role in a nuclear renaissance.
Making Reactor Parts with a Printer
3-D printing builds objects or structures by layering material in a programmed pattern. It is the three-dimensional equivalent of a machine that turns on-screen documents into printed pages.
The kind of 3-D printer that they sell in computer stores uses a resin that is good for making an ornate object the size of a key chain fob, but in industrial settings 3-D printers can use concrete and build an entire building, or powdered metal or metal wire that is fused with a laser into solid stainless steel. The technology can make precisely shaped small parts, sometimes more precisely than conventional fabrication.
Often it is cheaper to manufacture small parts in a shop, especially if you need multiple copies. So, why bother?
Due to years of little or no production, the nuclear supply chain has withered, meaning specific parts are both more expensive and harder to find. If a part is available from somewhere in the world, it may be fabricated only when the order is placed, and getting it delivered takes time. The plant may be shut down until the part is in hand. 3-D printing can help solve this issue by producing intricate parts for critical uses quicker than with existing supply chains.
But it takes time to prove that the materials are durable enough. A nuclear reactor is a harsh environment. Neutrons liberated by splitting uranium or plutonium sometimes go on to split another atom, or are absorbed by uranium, creating plutonium, but if that doesn’t happen, they hit atoms of other materials in the core and can damage them. So, engineers start with small samples of candidate materials, introduce them to the swarm of neutrons in the reactor, and see how they perform over time. At Ringhals, Framatome installed 3-D printed anti-vibration supports in the spring and summer of 2024, and most recently, filters that catch debris present in the cooling water.
Ringhals is not the first. In 2021, at the Browns Ferry plant, the Tennessee Valley Authority installed brackets that hold the fuel in place. They were manufactured at the Department of Energy’s Oak Ridge National Laboratory in a joint project with Framatome. The parts will remain in place for three fuel cycles, or about 6 years.
A year ago, Westinghouse, which is a major fuel manufacturer, said that it had fabricated nozzles for reactor cores that were 30 percent better at filtering out debris from cooling water, and that these had been installed in the core at the Southern Company’s Farley plant. Water circulates fast through a reactor, and if it carries debris, the debris can damage the fuel rods. The company said it had recently built its 1,000thcomponent that was manufactured with additive manufacturing for fuel for VVER-440 reactors. These are Soviet-designed plants in Eastern European countries that have recently turned to the West for fuel.
Reactor managers lose sleep over the possibility of needing a replacement part from a company that doesn’t exist anymore. They like the idea of a part that can be fabricated on site from a computer file that can be sent over the internet.
But 3-D printing is not just useful for old plants that require new parts. Additive manufacturing is proving quintessential to the new wave of modular and advanced reactors.
Oak Ridge has been active in additive manufacturing techniques that it believes will be useful for advanced reactors. Micro-reactors, according to lab scientists, will need embedded sensors, like fiber optics, to measure temperatures and strain. The lab has embedded fiber-optic sensors in metals commonly used in reactors, including stainless steel alloys, copper, and aluminum. The sensors are put into machined cavities, which are then covered with foils that are zapped by microwaves to seal them in.
Last summer, NuScale Power, which has an NRC-approved design for clusters of small nuclear reactors, won a patent for using additive manufacturing to make steam generator components with embedded sensors. Battelle and the University of Idaho are seeking to patent for 3D fabrication of heat exchangers for nuclear plants.
Iowa State University researchers recently got a grant from the Department of Energy to explore using 3-D printing to make parts for reactor cores from tungsten. Tungsten works well in high-temperature environments and resists erosion. The experiments will begin with pure tungsten and move on to alloys, and the researchers will use artificial intelligence to analyze the results.
And China has used 3-D printing in a multi-stage process to make tritium, which can be used as a fuel in a fusion reactor. The printed product has embedded lithium, which is split by the neutrons to produce tritium. The conventional manufacturing process leads to a product that tends to crack when irradiated, Chinese researchers say.
Beyond What a Machinist Can Do
In addition to using 3-D printing to make specialty parts that are available commercially only with a delay, or not at all, the technique can also make parts that simply can’t be fabricated conventionally. BWXT has moved heavily into this area.
“We started looking at additive manufacturing to give our designers more freedom,” said Kate H. Kelly, director of Space and Emerging Programs at BWXT Advanced Technologies, which is developing nuclear rocket engines that are cooled by gas. The shapes include a three-dimensional lattice with complex twists and very thin ligaments. Commonly, such parts are made by machining (or carving out) the desired shapes from bigger pieces of material, but these are “things that you couldn’t machine out to get that level of precision,” she said.
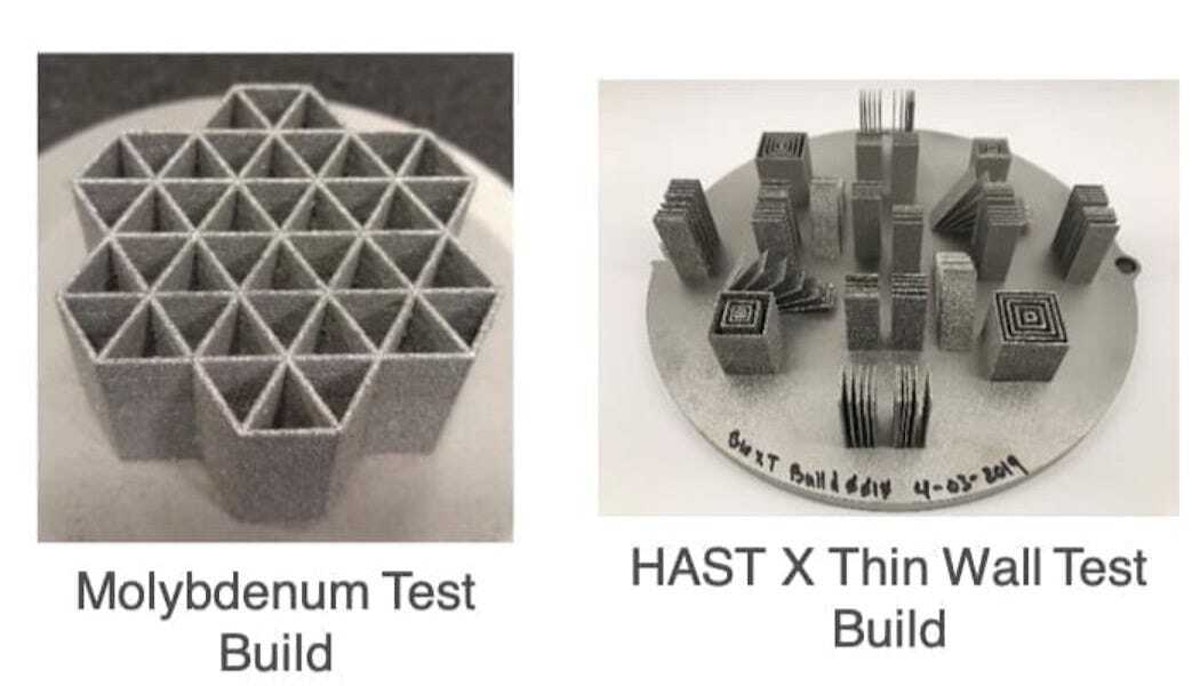
The material used for the component is often a brittle alloy, making it hard to machine, but easier to 3-D print.
There are several techniques for 3-D printing. One is using electron beam welding on a bead of alloys that are chosen because they can withstand very high temperatures, called refractory alloys. These are key because some advanced reactors are intended to operate at far higher temperatures than the familiar light water reactors, like Farley or Ringhals. BWXT is working on a rocket engine that will operate at more than 1700 degrees C, or 3100 degrees F. Lasers can also be used, to heat a powder and melt it into a solid.
And the components’ shapes, often designed using artificial intelligence, can be tweaked to allow optimum heat transfer. That can allow a smaller reactor, which is important for applications like space travel.
Researchers at the University of Tennessee are using the same logic. They have designed a graphite-moderated, gas-cooled reactor that is designed by artificial intelligence and then 3-D printed. The goal is a core with minimal temperature variation over its volume, producing as much energy as possible but with no spots that are too hot. The A.I. can try out designs with cooling channels that vary in radius over their length, and do not have to be straight. Then a 3-D printer fabricates it.
The NRC is paying close attention. Is the powder being fused into solid parts sufficiently pure? Was the fabrication process interrupted and resumed, which could affect quality? Is the geometry of the finished product accurate? And of course, what is the durability of these parts? The Electric Power Research Institute points out that among the complications, materials used in nuclear plants are generally covered by the American Society of Mechanical Engineer’s code, and approval by the code is long and costly.
Computer-driven 3-D printing isn’t the only modern technology that the nuclear industry is importing from other industries. Notably, it needs to replace analogue dials and gauges and mechanical switches in the control room with modern computerized sensors and controls, although there are regulatory barriers. The industry also needs to take advantage of advances in materials science in the years since the current fleet was built.
It is moving quickly in the direction of integration, both in new reactors and in reactors that have been running for decades longer than the new technologies have been around.