The Future of Nuclear at Sea
Shipyards around the world are already equipped to build small reactors and put them on ocean-going vessels. Let’s let them.
-
-
Share
-
Share via Twitter -
Share via Facebook -
Share via Email
-
Today, the world uses roughly 100 million barrels of oil and gas per day (BOE, barrels of oil-equivalent) for fuel alone. Although it has made great strides in replacing that direct use with electrification—the main way, so far, we’ve tried to move on from fossil fuels—much of the remaining consumption takes place in sectors that are hard or expensive to electrify.
These sectors include marine shipping, aviation, long-haul road-transport, heavy machinery, flexible power generation, and sectors for which fossil fuels are an input in industrial and chemical processes. In all of these, direct fossil fuel use is difficult to overcome due to existing infrastructure and assets, the properties of the fuels themselves, and fossil fuels’ low historical cost relative to that of alternatives.
In turn, while electrification has historically increased by about two percentage points per decade—today electricity stands at 20% of final energy use—it remains to be seen how fast it will continue in the next couple of decades, once all the low-hanging fruit is gone.
Even if we do somehow find a way to start transitioning the most difficult sectors and the electrification trendline rises to even double the historical rate, by 2050, electricity would still make up only 30 to 35% percent of end energy use. Much of the rest would be fossil fuels, which means that the total consumption of fossil fuel energy could well be even greater in 2050 than in 2020, since energy demand is still growing. And this is not even to mention the fact that electricity production itself is a significant source of emissions.
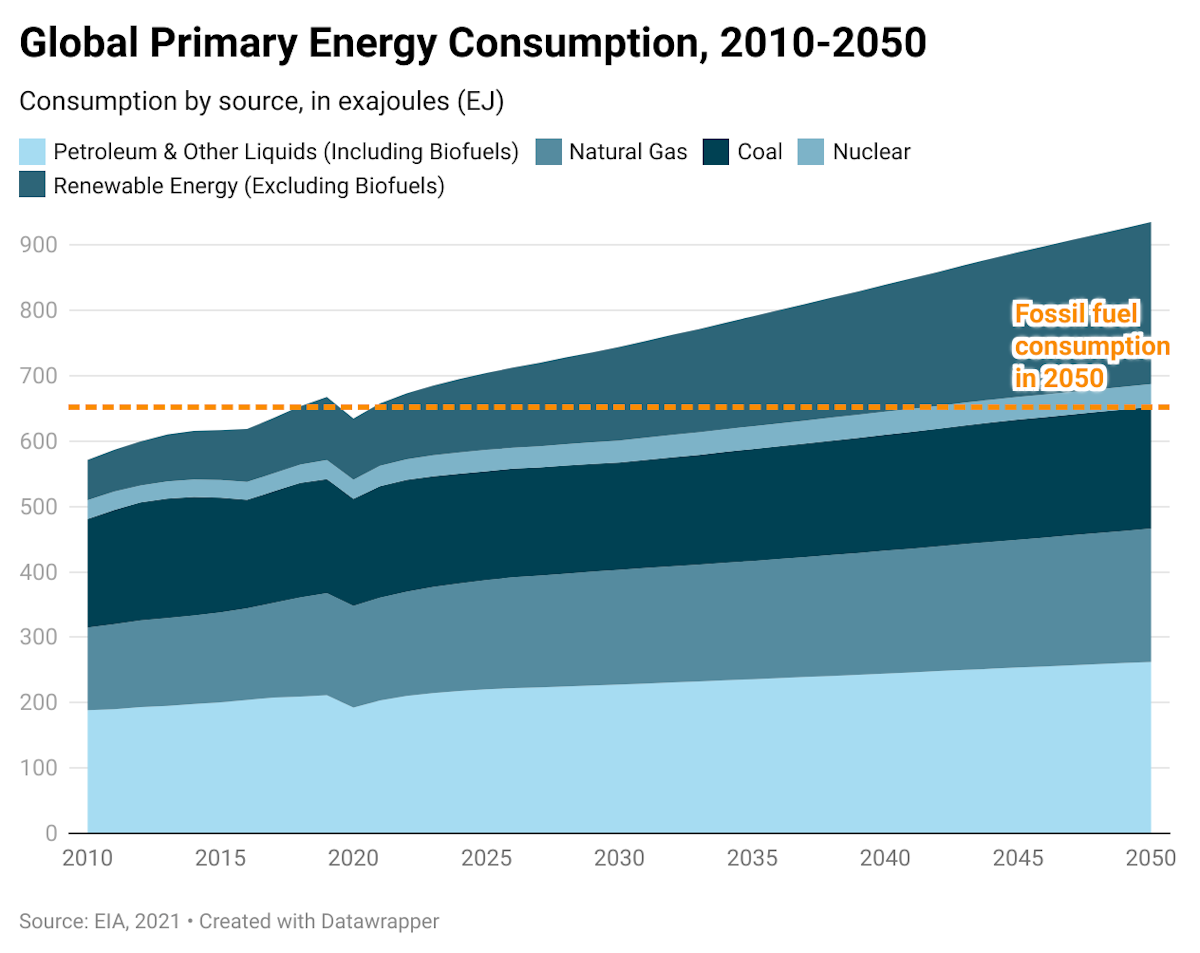
Facing these facts, if the world is to succeed in its climate efforts, while also increasing global energy supply to let developing countries grow their economies and developed countries maintain healthy ones, it will need to find solutions in addition to direct electrification.
One promising route is through clean hydrogen and other synthetic fuels, like ammonia, that produce zero emissions when burned. Synthetic fuels are generally made by combining hydrogen and nitrogen, or hydrogen and carbon. And, as long as the hydrogen and carbon atoms that are added to the mix also come from a clean source (the air, the ocean, sustainable biomass, and the like) rather than from fossil fuel, the production of t “e-fuel” is also clean. (For some purposes, hydrogen can even be used as an e-fuel by itself; but, in many cases, the best “plug-in” solutions are e-fuels that are chemically similar to its fossil counterpart, like those produced by combining hydrogen and other elements.)
The problem is, of course, scale. For e-fuels to replace fossil fuels en masse, we need to produce vast quantities and at very low cost. But how to get there?
Clean hydrogen can be made by separating hydrogen from oxygen through electrolysis, but this process takes electricity. Further, if this hydrogen goes on to be added to carbon or nitrogen to produce a synthetic fuel, more energy is required still. If we use every bit of electricity we currently generate around the world for these processes, we would still only be able to replace less than one-fifth of the fossil fuels we use with synthetics.
Further, it would be senseless to use our fossil-fuel-dominated electricity grid to power the creation of hydrogen fuel. But other fuel sources have drawbacks as well. The cost of wind and solar power has been decreasing, but their intermittency and low availability make them expensive choices for hydrogen production, especially since the electrolyzers and other processes in production facilities would only be able to run perhaps half the time, depending on the configuration.
Hydrogen produced using wind and solar power could cost somewhere between $3-7 per kilogram, depending on location and configuration. Yet, according to our estimates, clean hydrogen would only even start to replace some fossil fuels at around $2/kg. To use hydrogen to make competitive synthetic fuels, the cost would need to be closer to $1/kg.
To get to these low levels, the electrolysers need to be low-cost, high-efficiency, and operate continuously at a high capacity, not just when the wind blows or the sun shines. They’d need the kind of power that nuclear reactors generate; once turned on, reactors tend to operate at the same productivity for decades with pauses only for maintenance.
But new-build nuclear has not been particularly cheap lately, especially not in the West, where projects have stalled and gone overbudget, and nuclear has been struggling politically. Especially in the United States, low-cost natural gas has been the preferred option, despite nuclear energy’s zero-carbon emissions. And that’s why we need to rethink how we deploy nuclear power.
Why is Nuclear So Expensive?
To better deploy nuclear, we need to first understand why it is so expensive. The 2018 Nuclear Cost Drivers report, commissioned by the Energy Technologies Institute and produced in part by two of us through Lucid Catalyst, an international consultancy for decarbonization and clean tech, found several relatively straightforward reasons. These range from the building of a single reactor instead of many and the expenses that come from starting construction with unfinished, first-of-a-kind designs, to a lack of good supply chains due to a 20+ year hiatus in building new nuclear and inexperienced project management and regulators.
Building the same reactor at the same site with the same crew multiple times in a row is a clear way to bring down costs. But a big remaining chunk of the expense would still be that constructing something large and complex on-site is relatively inefficient and expensive.
Indeed, large infrastructure projects, where we drag materials, components, and thousands of people from all over the world to a site—often in the middle of nowhere—is among humanity’s least productive ways of building things. Sometimes it can’t be helped: a bridge, an airport, or a subway needs to be built where it needs to be used. But inefficiencies related to siting certainly contribute to high expenses.
Manufacturing in a factory-like environment, on the other hand, is among the most productive environments in which to build large things like airplanes and ships. Many small modular nuclear reactors (SMRs) are also designed to be manufactured in a factory and then transported to a site for assembly, which should help cut costs.
But there is a slight chicken-and-egg problem here. A nuclear reactor vendor needs to have a reasonably fat order book to justify (and get funding for) the construction of a major manufacturing center for the reactors and their modules. And to get those orders in, one should have a high level of certainty on the design and the presumably low cost at which it can be built.
For now, none of the new reactor developers are at a stage where these issues are solved. But there is a way circumvent the chicken-and-egg problem altogether—and perhaps many of the other obstacles and bottlenecks standing in the way of deploying massive amounts of new clean, nuclear energy.
The solution? Design the nuclear power plant so that it can be built at a modern shipyard.
Shipyards build ships, of course. But they are more than that; in reality, they are manufacturing centers for all manner of extremely large, complex, and highly regulated items, such as oil drilling platforms, cruise ships, and other marine vessels. In addition to large things, shipyards specialize in constructions that are designed for extremely challenging environments and operations, such as submarines or ice breakers. Modern shipyards already have the professionals and the supply chains in place to deliver safe, reliable, and ready-to-go products at impressively high levels of quality control and assurance.
There’s no real reason that they couldn’t turn that expertise toward building modular reactors and assemble them into barges and other offshore platforms that could operate as offshore power plants—perhaps even offshore power plants linked directly to hydrogen and synthetic fuel production. At least this is what two recent studies led by Lucid Catalyst demonstrated.
In the first study, “The Missing Link – How Hydrogen-Enabled Synthetic Fuels Can Help Deliver the Paris Goals,” we did the math on the global need for clean, low-cost hydrogen and e-fuels, the cost reduction potential of shipyard manufacturing and off-shore siting, and the overall scalability of global shipyard capacity. We also looked at the potential of building “Gigafactories” at industrial sites like refineries to manufacture advanced reactors to be deployed right there at the site and to make clean hydrogen and other e-fuels at the scale of dozens of gigawatts.
The second study, “Rethinking Deployment Scenarios to Enable Large-Scale, Demand-Driven Non-Electricity Markets for Advanced Reactors,” commissioned by Electric Power Research Institute, went deeper and more technical on the potential of global shipyard industry, as well as the Gigafactory concept.
The main finding of both papers was that these novel deployment models look extremely promising—both for reduced costs down and scaled-up production.
Scale Today
Today, the world has around 280 shipyards, and they have been working at roughly 50% average capacity due to overcapacity compared to demand. If even a small part of this free capacity were harnessed into producing nuclear power plants of various configurations, we could add hundreds of gigawatts of clean, low cost, and reliable energy production to global production capacity each year. Indeed, a single shipyard in South Korea—which, to be fair, is a very large one, since it represents almost 5% of global shipyard capacity—could produce 40 ships with 500MWe capacity each, per year.
If we harness a larger chunk of idle shipyard capacity, we could perhaps even add 200GWe of new nuclear capacity each year. For context, the global nuclear fleet currently stands at just below 400 GWe capacity and supplies around 10% of world’s electricity.
By utilizing all most currently idle shipyard capacity where feasible—and perhaps building some new capacity or modernizing old shipyards—we could essentially decarbonize the fuels sector by midcentury if the cheap, zero-carbon nuclear pours energy into generating synthetic fuels.
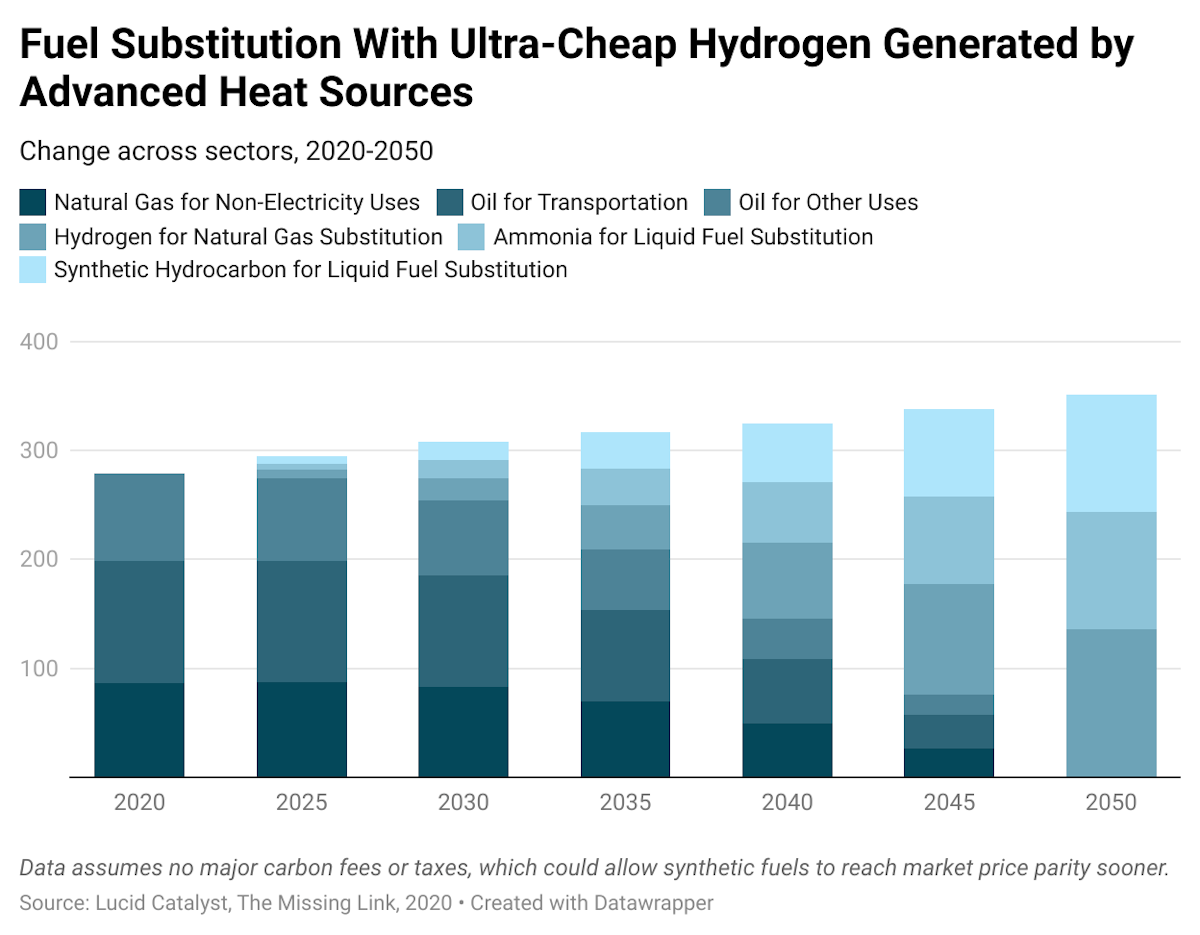
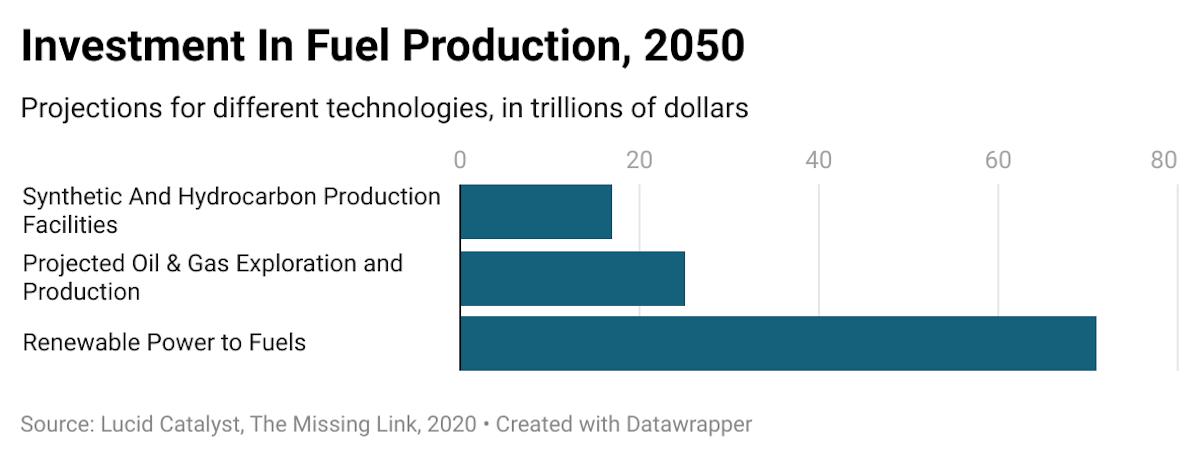
The Electric Power Research Institute study presented conceptual designs of large ships with 1.2 GWe of nuclear capacity, used for making both ammonia and jet fuel, as well as a design of a smaller 600 MWe multi-production platform that could produce electricity, ammonia, and desalinated water. The CAPEX (capital investment) costs for the Nth-of-a-kind vessels (so assuming licensing work was done for the first-of-a-kind) were around $1.5 billion, depending on the configuration.
The cost of the end-products from these vessels was competitive with the long-term average costs for their fossil fuel-based counterparts—even without carbon-taxes or fees that would increase their competitiveness even further. Ammonia could be produced below $250/ton ($290 for the multi-product platform), and jet fuel at below $85/barrel.
The larger, dedicated ships would each produce 1.2 million tonnes of ammonia per year and 4 million barrels of jet fuel per year, respectively. At the moment, the world uses 170 million metric tons of ammonia and more than 2 billion barrels of jet fuel per year.
Obviously, there would be bottlenecks as well; training operators, availability of uranium and uranium mining to feed the nuclear reactors, enrichment, and fuel fabrication capacity come to mind first. But it is a powerful fact that the manufacturing capacity, along with most of the necessary supply chains, already exists within the shipyard industry.
Why Finland is the Best Place to Get Shipyard Nuclear Started
So, where do we start? One idea is Finland, a proposal that Partanen looked into with his recent study, “Shipyard Nuclear in Finland.”
Besides the fact that one of us is Finnish and therefore had the interest in, the contacts for, and cultural context needed to write such a study, there are plenty of good reasons to start there. First is that Finland has a significant and high-quality maritime industry, with experience in building all kinds of special vessels such as ice breakers, even nuclear-powered ones (although the reactors themselves were installed in Russia), large offshore oil and gas drilling platforms, military vessels, and so forth. The needed expertise and infrastructure are largely already there, along with supply chains, a high-quality domestic metal industry, and machine workshops. Finland, even if it is a small country, still manufactures big components and machines and has substantial heavy industries.
Second, Finland also has a high-quality nuclear industry that has continued operating—and even building more—nuclear plants, even as most other Western countries have turned their backs on the technology. Every decade or so, the Finish nuclear industry has applied to get a “decision-in-principle” from the Finnish parliament to build a new reactor unit, and about 60% of the time, they have secured that political permission. That’s not perfect, and the approved projects have not been great successes. But the continued interest in building nuclear infrastructure at least places Finland ahead of many of its peers.
Finland has also had high public and political support for nuclear. In fact, both are now higher than ever. Public approval for building more nuclear is at 50%, with an additional 24% accepting current levels and only 18% saying nuclear should decrease from current levels. Most political parties are also constantly nudging their positions towards more positive outlooks, with the Finnish Greens becoming the first green party anywhere to dismiss its anti-nuclear stance and opt to support nuclear among other clean technologies. More than in other cultures, many people in Finland seem to recognize that nuclear is essential for meeting not only local climate targets, which are among the most ambitious in the world, but also global ones.
Like nuclear in general, SMRs have garnered support in Finland, including from most political parties. In 2020, the government started a major reform effort of nuclear legislation, in which SMRs and new uses for nuclear are among key topics. The country’s nuclear regulator is also looking into reforming its own safety regulations to be more suitable for small reactors and new use-cases. It seems that now, more than ever, is the time for novel ideas regarding nuclear, including shipyard manufacturing and offshore or nearshore siting.
In interviews of the Finnish shipyard and nuclear industries, politicians and ministry officials, the national regulator, and other key stakeholders in 2021 and 2022, it became abundantly clear that shipyard could be a significant opportunity. Finland has three large shipyards capable of designing and manufacturing floating nuclear power plants, and an additional one that already has the necessary licenses and certificates to produce nuclear-grade pressure components. Indeed, that shipyard (Pori Offshore Construction) was originally created to manufacture just those components for a planned nuclear power fleet in the 1970s. That buildout never materialized and, in a twist of irony, Pori had to pivot into oil and gas drilling platforms.
If these 4 Finnish shipyards used half of their capacity to manufacture and assemble floating nuclear power plants with 300-600 MWe of capacity each, they would be able to release somewhere between 1 to 2 gigawatts of new capacity, or some 15% of the current electricity consumption, every year within about a decade. Every year, then, they would roll out new nuclear capacity about equal to the energy produced by Finland’s Olkiluoto 3 reactor, a third-generation reactor that started producing power in March this year and took 16 years to build.
Shipyard nuclear would be a major boon, then, for Finnish carbon neutrality, as well as for the export of clean energy and the platforms for producing it, in Europe and beyond.
OK, But What is Shipyard Nuclear Going to Cost?
Initial estimates on the capital costs of these ships (Nth-of-a-kind) are at roughly €2,500 per kW (close to $2,500 at current exchange rates), with a levelized cost of electricity below €40/MWh. That is getting close to the cost of onshore wind; but, in this case, the money buys reliable, 24/7 energy with almost no land footprint. Indeed, the ships might take no land at all, given that they can be sited at sea, or in a harbor, depending on the application. Hence, they would not be in anybody’s backyard, would require much less preparatory work at the site, less concrete, and so forth. Power-production barges would likely be placed relatively near shore, and electricity transferred by underwater cable, although farther offshore, as with offshore wind farms, is also a possibility.
With costs this low, the market for shipyard nuclear energy could quickly expand from just power and heat into hydrogen and synthetic fuels. Hydrogen could be produced at costs below €2/kg and, with mass manufacturing, operational optimization, and advanced technologies, this cost could get close to €1/kg as the technologies and systems progress. Not only would this cost be low enough to replace hydrogen that is currently made from fossil fuels and used in oil refining and the fertilizer industry, but it could eventually replace fossil fuels themselves with synthetic, carbon neutral alternatives in uses where batteries and other direct electrification options are not feasible.
If this sounds like a moonshot, let’s come back down to earth for a moment. Marine nuclear, after all, is really nothing new. Hundreds of small marine reactors have been built and operated in the last 70 years, albeit mainly for military vessels. No doubt there are issues to be resolved in licensing, operating, and proving the safety case for commercial plants. And for international commercial applications, global maritime regulation and trade regimes would need to get up to speed. But, at least according to the 2022 IAEA book on Nuclear Law, the legal infrastructure is at least in place for pilot projects. And these pilot projects themselves would have a substantial technical history of maritime nuclear to start from.
It is, of course, still too early to say whether Finnish actors will move forward with this particular concept, but the initial interest from stakeholders with whom we’ve discussed the project has been good, and plans for next steps are underway. For example, the state innovation and export technology fund, Business Finland, has shown significant interest in providing funding for programs aimed at the commercialization and creation of this new industrial sector in Finland.
Internationally, too, there has been increasing interest in floating power plants and offshore/nearshore applications from reactor developers in the larger markets. The Russian Akademik Lomonosov, a floating nuclear power plant, has already been in operation for a couple years, and both the U.S.-based ThorCon and the Danish Seaborg have designed their reactors as shipyard-manufactured barges from the start. Others, like Core Power, NuScale, and KEPCO are working on various marine applications, as are the big Chinese nuclear companies. Shipyards have started to awaken into the opportunity as well, signing MoUs with reactor developers to eventually build these ships.
Obviously, all the best-case scenarios we’ve set out assume that governments, utilities, oil companies, and shipyards seize the opportunity. And that will, of course, be up to them—and to the individual political, economic, and regulatory conditions they face. But what we can say is that the opportunity is there, and it is massive. While the idea of manufacturing hundreds of gigawatts of nuclear plant capacity per year sounds almost impossible in the context of the current nuclear industry, this particular way of doing so at least replicates something that we already do in other industries. We already make thousands of passenger airplanes and ships per year. We already make millions of tons of ammonia to help feed us, mainly from fossil natural gas, and use billions of tons of fossil fuels in many different purposes annually.
The urgency and scale of the climate emergency demands that we leverage this existing know-how, infrastructure, network of global supply chains, and human ingenuity to transform our global energy system to keep the global economy moving, protect the wellbeing of all people, and support the health of the planet.