Are There Enough Critical Minerals for Hydrogen Electrolyzers?
Why Future Hydrogen Production May Need a Minerals Supply Boost
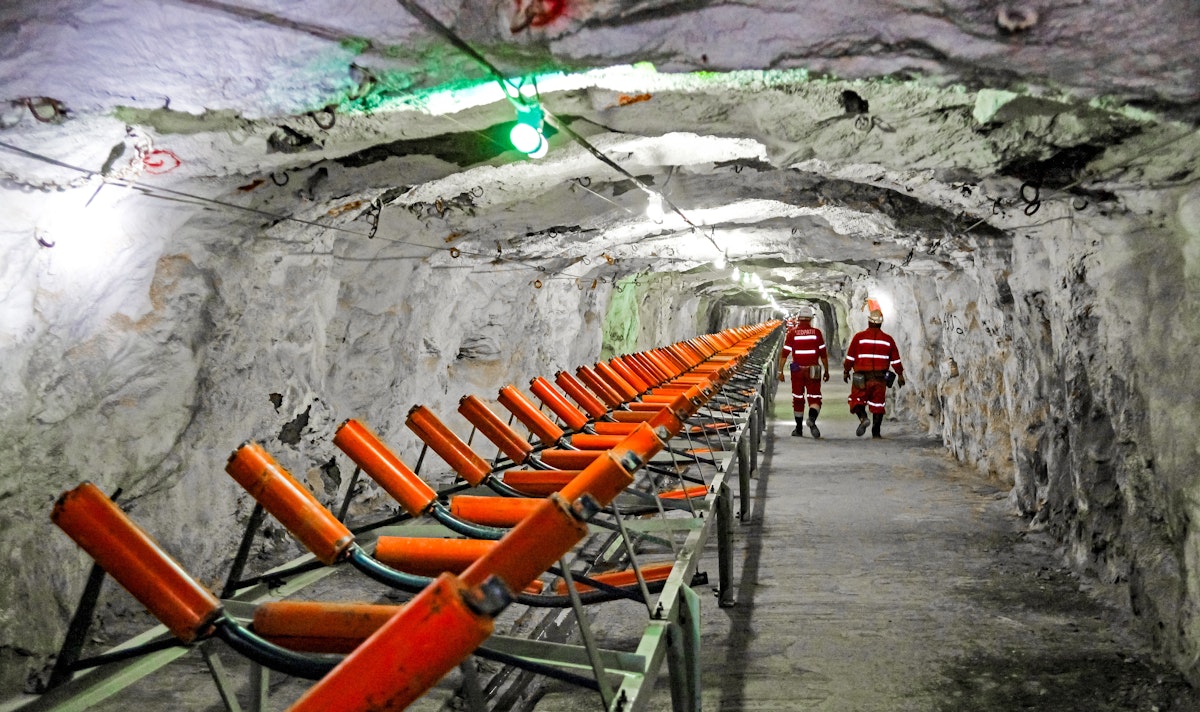
-
-
Share
-
Share via Twitter -
Share via Facebook -
Share via Email
-
The world is in a rush to produce massive volumes of hydrogen. If properly executed, it could be the key to the last stretch of global decarbonization. Electrolyzers, modular units that use electricity to split water molecules to produce hydrogen, are the primary technologies for clean hydrogen production. Unfortunately, progress thus far is wholly insufficient. Currently, the total global electrolyzer capacity is less than 3 gigawatts (GW), a mere fraction of the thousand-plus gigawatts needed for a global decarbonized energy system.
Clean hydrogen enables the development of decarbonization technologies like low-carbon ammonia fertilizer or hydrogen-powered fuel cell vehicles (FCVs). Hydrogen also represents a possible replacement for fossil fuels for other hard-to-decarbonize industrial processes requiring high heat.
As hydrogen demand increases, governments are increasingly prioritizing the electrolyzer sector. The Biden administration granted over $500 million to the Department of Energy (DOE) to build out domestic energy supply chains, including electrolyzer manufacturing capacity. Both the Bipartisan Infrastructure Law and the Inflation Reduction Act (IRA) amount to massive investments into clean hydrogen production, totaling about $21 billion. In 2023, the Japanese government committed about $54 billion over the next 2 decades for clean hydrogen production, including assistance to Japanese electrolyzer manufacturing companies. In 2020, Canada announced a plan to ramp up its electrolysis facilities to achieve a target of using hydrogen for 30% of the country’s energy supply by 2050.
But there’s one thing missing from these clean hydrogen policies—the critical minerals required to make them work. Estimates for increased clean hydrogen supply can only be true if there are sufficient electrolyzer material production first. This raises the question: are there enough critical minerals to fulfill the required future electrolyzer capacity needed to produce clean hydrogen? And if so, what are the bottlenecks that could impede electrolyzer manufacturing?
Our analysis finds that the majority of supply-constrained precious minerals for electrolyzers are due to market and economic barriers that limit production rates. Policymakers should prioritize mitigating these barriers with stronger critical mineral supply initiatives including production incentives, supply chain diversification, and material use optimization.
Current Material Requirement of Electrolyzer Capacity
The critical material demands depend on the electrolyzer type. There are currently three main types of electrolyzers with more than 1 GW/yr of capacity being manufactured annually: Alkaline, proton exchange membrane (PEM), and solid oxide electric cells (SOECs). Fuel cells operate similarly to electrolyzers, but instead convert supplied chemical energy into electricity. Table 1 highlights the current material requirements for electrolyzers and fuel cells on a tons per gigawatt basis.
Alkaline electrolyzers are the most common type of electrolyzers and the most technologically mature. It uses an alkaline electrolyte solution typically made up of potassium or sodium hydroxide. Increased hydrogen demand, mainly from the chemical industry, led to a ramp up in alkaline electrolysis usage in the mid-20th century. Alkaline electrolyzers also currently cost less than competing technologies, partly owing to their use of common metals such as iron and nickel for their electrodes.
PEM electrolyzers are the second most common type. In PEM electrolyzer cells, the electrolyte is a special type of plastic-like material (or polymer membrane) which selectively allows the passage of hydrogen ions from the anode to the cathode. PEMs utilize platinum group metals (PGMs) including palladium and iridium as catalysts which increase the rate of the chemical reactions. PGMs are also more expensive as they are more precious relative to more common metals.
SOECs use a solid ceramic-like material as the electrolyte, and operate at much higher temperatures (700 - 800℃) to produce steam that will eventually combine with electrons to form hydrogen gas. They require rare earth elements (REEs) like yttrium and lanthanum, typically used to optimize the chemical reactions between the electrolyte and the electrodes. SOECs are the most expensive due to the energy required to operate at such high temperatures, and the rare earth metals used in their structure. But these units also operate at the highest efficiencies (>80%) compared to Alkaline (51%) and PEM (58%).
Hydrogen fuel cells also require critical minerals, which consume hydrogen fuel and produce electricity. In a hydrogen fuel cell, a catalyst splits hydrogen molecules into protons and electrons. The electrons follow an external circuit which generates electricity. The protons and electrons eventually combine with oxygen to produce harmless byproducts: water and heat. The catalyst is typically platinum which encourages the release of electrons from the hydrogen molecule that will form an electric current. Fuel cell technology is mainly implemented in electric vehicle applications—like the Toyota Mirai—with limited success. However, hydrogen fuel cells could prove more competitive in other areas such as heavy transportation and stationary applications.
Material Requirement of Future Electrolyzer Capacity
In this analysis, we use future electrolyzer and fuel cell capacities to derive material requirements for both technologies. Modeling estimates of global electrolyzer capacity in 2050 range widely between 1,400 and 7,800 GW, with some highly aggressive 100% renewables-only pathways arriving at values of 16,700 GW or more. The specific models used for this analysis are the IEA SDS scenario, IRENA, and the Economic Transitions Commission (ETC). The models’ respective electrolyzer capacities are shown below in Figure 1 for years 2030, 2040, and 2050.
We assumed a future electrolyzer market share of 40%, 40%, and 20% for alkaline, PEM, and SOEC electrolyzers respectively to derive each material requirement. This assumption reflects overall optimism for the future of electrolyzers while avoiding speculation on whether alkaline or PEM electrolyzers will dominate industry share. The IEA SDS was used for the future fuel cell capacity. The 2022 production rates, shown in Table 2, are held constant for future assumed production. Each assumed market share (or capacity) is combined with 2022 production to estimate each study’s material requirement for each year, as shown in Table 3.
Based on this analysis, alkaline sectoral growth will add modest demand for more common metals like nickel, aluminum and steel. For instance, aluminum requirements for alkaline electrolyzers might amount to at least 300,000 tons to fulfill the projected 2050 capacity based on the IEA SDS scenario. However, this is negligible compared to estimates of 58-380 million metric tons of aluminum (1-5.5 years’ worth of current global production) potentially required for solar and wind farms over the same period. Assuming 4 tons of bauxite produces 1 ton of aluminum and bauxite production rates remain at 2022 levels, even the upper bound for aluminum consumption in electrolyzers (1,560,000 tons cumulative) would total less than 1% of cumulative annual production of mined bauxite from now to 2050.
SOEC critical minerals will also be sufficient, including the more precious REEs like lanthanum and yttrium which will both require less than 3% of the cumulative production from now to 2050. However, PEM critical minerals are the most constrained based on current production rates. Policymakers should devote more attention to these metals which could bottleneck electrolyzer deployment.
For the scenarios examined, more vulnerable metals include platinum, palladium and iridium. Cumulative 2022-2050 PEM electrolyser usage of platinum and palladium both total just under 20% of estimated cumulative mine production, assuming 2022 annual production rates. However, achieving 20,000 GW of hydrogen fuel cell capacity by 2050 would consume about 5,800 tons of platinum, the equivalent of 31 years’ of 2021 global platinum production. Thus, platinum production could fall short of clean energy transition needs if manufacturers are not adequately prepared to fulfill demand.
Iridium is the most constrained of all the electrolyzer materials, requiring between 2-fold to more than 10-fold of cumulative mine production between 2022 and 2050 assuming the 2022 annual production rate. Annual production rates must greatly increase to meet the massive demand growth for these metals. Other factors such as supply chain overconcentration may impose additional constraints, due to increased risk of production and supply chain disruptions.
At the same time, future platinum, iridium, and palladium demand in hydrogen technologies may be overestimated if material use efficiencies continue to improve over the next few decades. Reducing PGM use in electrolyzers is already a major priority focus of ongoing R&D and commercialization efforts. However, current production of electrolyzer and fuel cell critical minerals is sufficiently vulnerable such that supply chain constraints could worsen, or persist for longer than anticipated. Policymakers should plan accordingly to prepare to accommodate the full scale of potential future electrolyzer material demand.
Current Bottlenecks of Electrolyzer Material Production
As is the case for many clean technologies, critical mineral production will heavily influence the cost and scale of future global electrolyzer deployment. This is particularly true for PEM and SOEC electrolyzers, which utilize platinum group metals and rare earth elements respectively. PGMs and REEs are both expensive categories of raw material inputs with relatively limited, over-concentrated supply chains.
Current, PGM and REE supply chain challenges present potential constraints for future PEM and SOEC electrolyzer deployment. These barriers appear to be driven more by economics rather than limited geological stocks. First, the near-term stock available for societal use is limited to geological reserves that are economically viable to extract with today’s technology at current commodity prices. Next, the rate at which these underground stocks become available to society is limited by current mining rates, which are not all optimal. Finally, a relatively small number of suppliers produce these metals today, limiting the rate at which the industry can expand in the near term. For instance, the majority of the world’s production of both platinum group metals and rare earth elements is concentrated in just a few countries—South Africa, Russia and China—increasing the risk of unpredicted disruptions to the supply chain.
The select number of countries with an effective monopoly on the majority of the supply chain poses an ongoing risk for the electrolyzer industry. More than 70% of global platinum supply and over 80% of global iridium supply concentrated in South Africa. A recent Rystad analysis anticipates that platinum and iridium prices may rise due to South Africa’s high energy costs, driven by a fragile electricity network dependent on “aging, fault-prone coal-fired” plants. This is on the heels of South Africa’s PGMs production 2022 shortfall due to operational issues including electricity outages and processing plant closures. Iridium is currently only produced as a by-product of other mining, such that future demand growth might require sizable investments for dedicated production facilities.
Similar geographic dependence is shared by the SOEC supply chain. In 2022, China supplied about 95% of the required rare earth metals for SOEC electrolyzers, including lanthanum and yttrium, and produced 70% of global rare earth elements. Other nations such as the US, Myanmar and Australia produce REEs in much smaller quantities, with the US producing the second most in 2021 at just 15.5% of the overall global rare earth element (REE) supply. Addressing these constraints will require a combination of policies to support mining production, supply diversification, and research and development.
Looking Ahead
Securing such a massive scale up of electrolyzer manufacturing will require an equally massive increase in electrolyzer raw material production. Policymakers must work internationally to expand mining production and processing capacity, while supporting continued exploration for PGMs and REEs.
Robust policy interventions can produce rapid changes in critical mineral production. Once the top global supplier of rare earth elements, the US mining industry in recent decades largely shifted to importing REEs instead. But increasing concern over the risks of a heavily import-dependent mineral supply drove the Biden administration to prioritize production of key minerals as part of broader national clean energy policies. The Inflation Reduction Act (IRA) allocated billions of dollars to the acquisition of critical minerals essential to all clean energy technologies, and included tax credits that reduce domestic REEs developers’ production costs by up to 10%. Such interventions have powerfully influenced the economic outlook for domestic US REE mining and refining operations.
Diversifying the mining supply chains for electrolyzer materials would decrease risk arising from supplier overdependence and may help reduce hydrogen technology costs in the long term. Countries prioritizing electrolyzer deployment must also consider the sources from which their constituent minerals are extracted. Certain countries currently dominating critical mineral supply chains are also commonly associated with higher labor and environmental risks. Other states must therefore prioritize ramping up domestic critical mineral production to mitigate these risks.
On the demand side, electrolysis and fuel cell industries must continue to find success in reducing metal requirements. Nickel use in state-of-the-art alkaline electrolysers recently fell from over 1 tonne to 800 kg per MW. Toyota’s 2014 first-generation Mirai fuel-cell vehicle used three-quarters less platinum per kW than its 2008 prototype. The 2020 second-generation Mirai reduced this by another third. Such reductions lessen environmental impacts associated with extraction and reduce mineral supply constraints.
Further electrolyzer research and development could mitigate these constraints even further. For example, the use of anion exchange membranes (AEM) could eliminate the need for metals like platinum and iridium altogether. AEM electrolyzers, similar to PEM electrolyzers, utilize a polymer-like membrane to allow the passage of hydroxide ions that convert into hydrogen gas. AEM electrolyzers could achieve higher efficiency, with potentially lower costs from eliminating precious metal needs.
Recycling may also offer a source of metals long-term, depending somewhat on the degree of metal degradation by the end of the electrolyzer lifetime. Some companies are targeting deployment and utilization strategies for PEM electrolyzers that could enable recycling rates greater than 90% for platinum and iridium. Techniques to enable the reuse of PGMs and other critical minerals could advance further over time.
But, recycling is generally not as economical as a source of raw materials compared to extracting new minerals. Some minerals, particularly REEs, are difficult to recycle because they are hard to separate from other minerals. Recycling REEs is quite an energy-intensive process for what may be less than an ounce of metal. High metal purity is another priority as to whether or not recycling is worthwhile. Numerous organizations are working to improve recovery techniques which better preserve usable precious metals such as iridium. In the long term, countries may need to further improve and incentivize recycling supply chains to make secondary metals more competitive relative to new mining. Recycling cannot meet all hydrogen technology critical mineral needs, but could certainly alleviate future constraints as a growing secondary source to support increasing deployment.
Overall, the future electrolyzer industry’s success will depend on overcoming bottlenecks over the course of long-term supply chain expansion. To meet even the lower bound of 1400 GW of capacity by 2050 estimated in the IEA’s SDS pathway, countries would need to at least triple the annual electrolyser deployment rate relative to last year’s total nominal manufacturing capacity of 11 GW. This will require a tremendous effort to mitigate risks and pursue continued technological innovation to promote low-cost, large-scale production. At the very start of the supply chain, increased mining production is critical for meeting anticipated mineral demand, especially for PGMs and rare earths, while simultaneously ensuring such production does not produce unfair practices or disproportionate environmental costs.
Our analysis demonstrates that generally, there are ample materials to meet electrolyzer deployment targets. Rather, nearer-term decisions regarding policy and production will play the more decisive role in achieving the required scale. If governments are serious about clean hydrogen production, electrolyzer critical mineral acquisition should become an urgent priority.